SUSTAINABILITY REPORT 2024
The ORI Martin 2024 Sustainability Report is now online.
“A document that reflects our ongoing commitment, built on tangible actions, and driven by the desire to combine industrial excellence with care for our people and the planet — creating shared value for the community, the environment and future generations.” – Carolina de Miranda, Sustainability Manager, ORI Martin
The Group Sustainability Committee, our Sustainability Framework, the ORI Academy: 2024 marked a pivotal year in our journey towards sustainability, innovation, process efficiency and environmental impact reduction.
All of this – and much more – is presented in our latest Sustainability Report.
We firmly believe this is the right path forward, and our commitment continues.
Download:
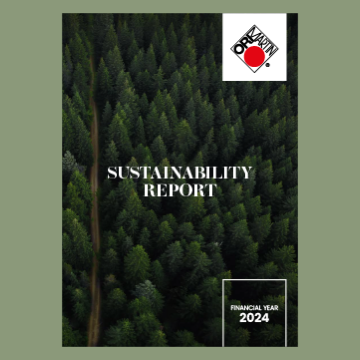
Decarbonisation Plan
In 2023, ORI Martin formally defined its decarbonisation strategy.
The plan identifies an emissions reduction target in terms of tonnes of direct and indirect CO2e (Scope 1 and Scope 2) per tonnes of billet produced.
The reduction target is in line with the ‘Science Based Target Inititiative’ (SBTi), and aims at a 30% reduction on Scope 1 and 2 emissions by 2030, using 2018 data as a baseline.
The second target for 2030 is the use of at least 25% of green energy. In order to meet this targets, a series of actions have been planned, relating to energy efficiency and renewable energy.
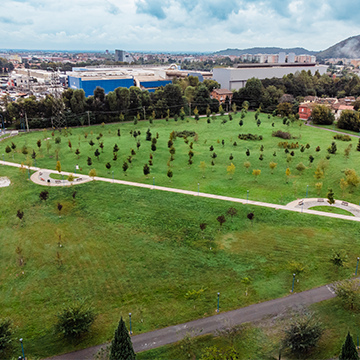
CIRCULAR ECONOMY
The use of EAF furnaces instead of Blast Furnaces, allows the use of ferrous scrap as a raw material, giving an infinite life cycle to steel products that will become scrap again and then again raw material.
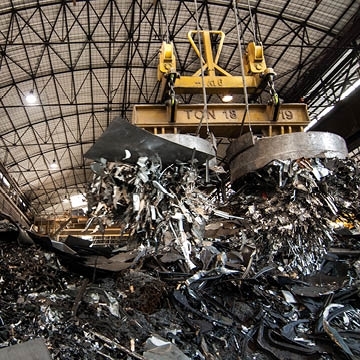
I RECOVERY
The project is worth over 12 million euros and has been active since 2016, the first of its kind in Italy; it was implemented in collaboration with technical partners such as Tenova, Turboden and A2A.
The I-Recovery system allows to convey the large amount of heat contained in the fumes of the electric arc furnace into a system that avoids its dispersion.
In fact, the heat is recovered through the generation of steam, which is stored and used as dual purpose:
it is either transformed into thermal energy to be fed into Brescia district heating network or into electricity through an organic fluid turbine (ORC).
Thanks to this technology, I-Recovery supplies about 10MWt for heating in the winter period, equivalent to the annual needs of about 2,000 families. In summer, however, it produces clean electricity (about 1.8 MWe), equivalent to the needs of about 700 families.
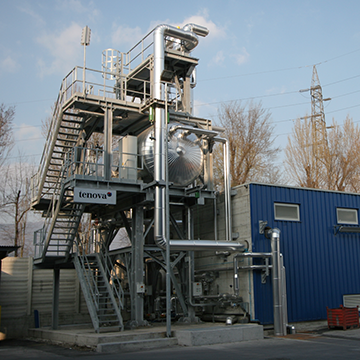
12
MLN/€TOTAL
INVESTMENT
52
GWHANNUAL HEAT
RECOVERY
CAPACITY
10,000
TON CO2HEATLEAP PROJECT
The HEATLEAP PROJECT is realized in partnership with Turboden, the heat pump provider and in collaboration with other important companies such as A2A, the CSMT - Centro Servizi Multisettoriale Tecnologico, Rina consulting and Cogen Europe and financed by the European Commission on the LIFE 2020 call.
Out of a total cost of 6.5 million Euros, the HEATLEAP project received a grant of 2.5 million Euros from the European Commission on the LIFE 2020 call for proposals. The project has officially started on 1ST June 2020 and will last two and a half years.
The main objective of the project is to recover most of the thermal waste of steelmaking, which would otherwise be dispersed in the environment.
Thanks to a special, large heat pump with a size of up to 7 MWth, the heat is recovered at a low temperature (about 70°C) and then taken up to an adequate temperature (from 95°C up to 120°C) to then be put into the town district heating network.
>> Read the news for further information.
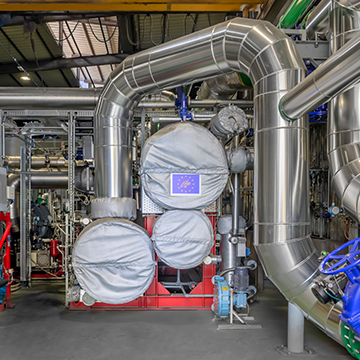
5,000
TON CO2ABOUT
7
MWTHENERGY
EFFICIENCY
CORALIS
To promote and develop the circular economy, ORI Martin has joined the Coralis project, funded by the European Union under Horizon 2020. This programme focuses on the valorisation and reuse of metal waste, aiming at a reduction of material sent to landfills.
The waste produced in the industrial areas of the three countries participating in the project (Brescia, Italy, Frovi, Sweden and Escombreras, Spain) is treated with advanced technologies and transformed into raw material, to be recovered or reused in other production processes with a view to synergy and circular economy.
As part of a consortium of 29 companies, research centres, and universities, ORI Martin plays a key role in recovering metallic residues rich in powders and oxides, which are then reintroduced as raw materials (iron) into the steelmaking process.
CONSTEEL TECHNOLOGY
ORI Martin uses the Consteel technology, which allows the continuous loading of the scrap into the electric arc furnace through a special mechanical conveyor that allows the preheating of the scrap with greater energy efficiency.
Furthermore, this technology brings considerable advantages both for the lower consumption of electricity and for the problems related to the environmental impact (reduction of the plant’s acoustic impact and secondary emissions due to the reduction of scrap loading with buckets) and for a better control of the radioactivity of the incoming scrap.
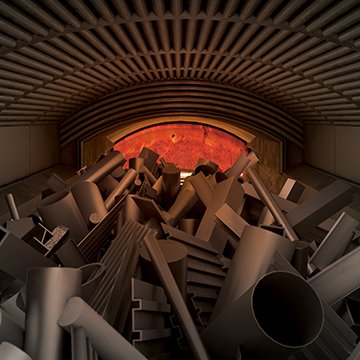
OF EAF DUST
DISPERSION
RECOVERING
IMPACT
REDUCTION
WATER RECYCLING
Water is amongst the most monitored resources by ORI Martin as a vital asset to be preserved. Large amounts of water are required to cool the furnaces in steelmaking.
Water that comes into direct contact with steel during the cooling phase require a treatment to eliminate metal scale and oils. In such case, water is conveyed to special collection tanks to be sent to the purification plants (one for the steel shop and one for the rolling mill), equipped with settling tanks and sand filters.
The continuous investments in water recycling allowed to reduce by more than 60% in 20 years the specific consumption of water per ton of hot rolled product.
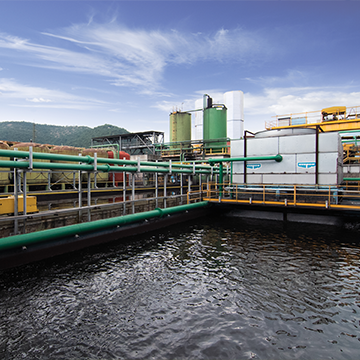
-64%
FRESH WATERCONSUMPTION
IN THE LAST
20 YEARS
RENEWABLE ENERGIES
Reducing environmental impact for ORI Martin also involves generating electricity for self-consumption thanks to the numerous solar panels installed on the roofs of the group's real factories.
By 2024, ORI Martin has about 20 MW of self-generated renewable energy.
In addition, in 2019, the company signed a renewable power purchase agreement (PPA ), which will ensure that at least 10 % of the plant's electricity supply will come from renewable sources, specifically photovoltaic systems.
Moreover, with a view to increasing its percentage of green energy as much as possible, the company has a project-under development-that involves the installation of an agrivoltaic plant of about 6 MW on an eight-hectare plot near the Ospitaletto plant.
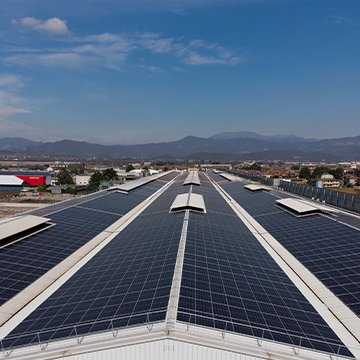
EAF GAS TREATMENT
Brescia plant is part of the Emission Trading System (EU - ETS), an instrument set up by the European Union Directive 2003/87, aimed at monitoring and progressively reducing greenhouse gas emissions from the highest energy-intensive industrial sectors.
The ETS system, designed to tackle climate change, rests its foundations on a mechanism called “cap and trade”. This mechanism caps the presence of a maximum limit of tons of CO2 that industrial plants subject to this system can emit. Based on the actual quantity emitted and declared annually, the subjects receive or purchase emission quotas that can be exchanged through a sale on the global CO2 market.
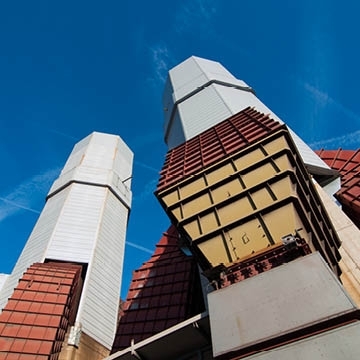
7
MLN€INVESTMENTS
ON NEW
FILTER
SYSTEM
2
MLN€SPENT EVERY
YEAR FOR EAF
EXHAUST GAS
CLEANING
100%
RECYCLINGOF EAF DUST
<1
mg/Nm3EMISSION OF
PARTICULATES
NOISE REDUCTION
ORI Martin pays great attention to the acoustic impact caused in the surrounding area by the activities of the plant and the movement of heavy vehicles.
For several years, the Company has been intervening in the most critical areas of the plant by installing soundproof walls and doors with the aim of containing the noise produced by the systems.
These interventions provided compliance with the noise pollution limits set by the Municipality.
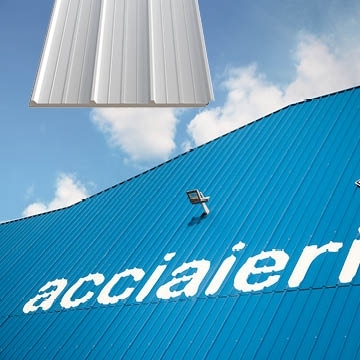
1.5
MLN€INVESTMENT
OVER LAST
3 YEARS
STONE WOOL
INSULATION,
OVER
10
CMTHICKNESS
PANEL
20,000
SQM OFSURFACE
Environmental Product Declaration (EPD) certification
As a further step towards an environmentally sustainable production, in 2022 ORI Martin has concluded the Life Cycle Assessment (LCA) of its steel products in order to register them for the Environmental Product Declaration (EPD) certification.
The Environmental Product Declaration (EPD) is a voluntary declaration describing the environmental performances of products in compliance with the ISO 14025 international standard. The EPD is the main environmental certification in the Italian and European context and represents an essential step to declare the sustainability performances of production.
ORI Martin S.p.A. received the EPD for the following products:
• Steel billets
• Hot-rolled wire roads and bars
• Annealed wire-roads and bars
• Quenched and tempered bars
Download:
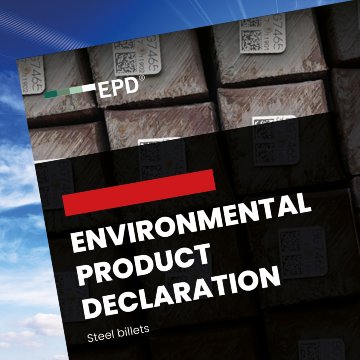
WASTE RECYCLING
Several research projects are underway to develop new systems, new applications and new patents for the recovery of steel mill slag and waste products.
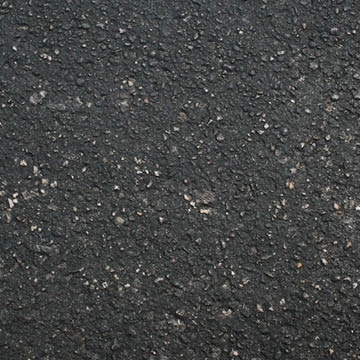
RAMET consortium
ORI Martin has participated in the RAMET Consortium (www.consorzioramet.it) since its foundation. This brings together 21 metallurgical companies from Brescia in a common project for the study and monitoring of the environmental impact of the production activities both on the workplace and the vicinity. The consortium's activity is carried out through the implementation of modeling studies relating to the presence of pollutants in the air, environmental chemical analyses and studies on micropollutants, as well as research on the treatment, disposal and reuse of waste.
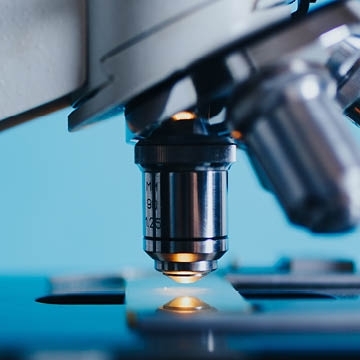
ESTEP
The acronym of "European Steel Technology Platform", a non-profit organization in which ORI Martin has participated, together with other electricity cycle producers, since 2020 in the "Clean Steel" project with the aim of defining the guidelines for the production of clean steel from electric furnaces at a European level.
www.estep.eu
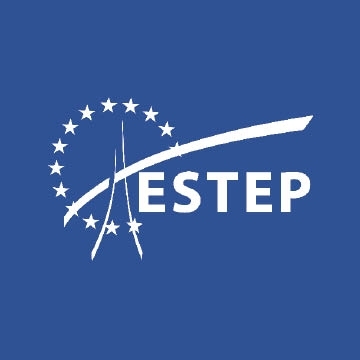